Unik Techno • August 20, 2020
What happens if lead acid battery runs out of water?
What happens if lead acid battery runs out of water?
A lead acid battery has positive & negative plates fully immersed in electrolyte which is dilute sulphuric acid.
The concentration of electrolyte is defined & specified for batteries of different applications based on the application & in line with national & international standards.
This concentration is expressed as specific gravity.
This specific gravity is usually determined at design stage by battery manufacturers with relation to the volume of electrolyte which can be accommodated in a cell. The specific gravity is always in a defined range with the maximum specific gravity specified in such a manner so that it does not accelerate corrosion of battery components & allows for release of sulphate from the plates when a battery is on charge. The minimum specific gravity is also such that it retains the conductivity of electrolyte so that there are no problems to charge a fully discharged battery. Thus the volume & concentration of electrolyte form part of the design of battery.
As regards battery plates the active materials of the plates are decided in such a manner that the quantity of active materials as well as surface area of the plates decide battery capacity.
When the level of battery electrolyte reduces to an extent that the top portion of the plates are exposed - a situation is created wherein a certain portion of the plates do not take part in the reaction.
This leads to reduction in battery capacity. This is undesirable & hence it is not recommended to allow the battery to run out of water.
Regular topping up with distilled or demineralized water ensures that level of electrolyte is maintained. Evaporation of water component of battery electrolyte has to be compensated by topping up with water on a regular basis at defined intervals.
Another effect of reduction of electrolyte due to evaporation of water is increase in concentration of electrolyte i.e. increase in specific gravity. An increase in specific gravity of electrolyte with plates not fully immersed in electrolyte results in heating up of cell on charge. The battery can get damaged since corrosion of internal components used in battery manufacturing is accelerated in the acidic electrolyte at elevated temperatures.
A physical effect of reduction of water is heating up especially during the last stages of charging or in case of an undesired overcharging. Electrolyte also acts as a coolant though this may not be its main purpose for its presence in a battery. Hence the problems of thermal runaway faced by sealed maintenance free (SMF) or valve regulated lead acid (VRLA) batteries is not a phenomenon faced by designers of flooded electrolyte lead acid battery designers.
Finally coming to the main question as to what happens when a lead acid battery runs out of water – totally i.e. electrolyte has fully dried up or battery has been tilted or stored upside down due to which the electrolyte has spilled. Please note that we must not remove acid completely from flooded electrolyte lead acid batteries once it has been filled with acid & charged.
A lead acid battery consists of a few major components viz. the positive electrode, negative electrode, sulphuric acid, separators & tubular bags.
In charged condition the positive electrodes are lead dioxide and negative electrodes are sponge lead.
Sponge lead is highly reactive in the presence of moisture & oxygen and gets converted to lead oxide. In the process of conversion to lead oxide it gets discharged & heated up.
Hence it is necessary to ensure that the acid is not spilled or drained from a wet battery once it is filled and charged.
As and when a battery filled with acid is drained of acid the wet moist negative electrodes come in contact with atmospheric oxygen. An exothermic reaction takes place releasing an enormous amount of heat thereby discharging the negative plates (electrodes) and oxidizing the sponge lead to lead oxide.
During this exothermic process of heating up of the negative electrodes, the other components within the cell i.e. separators, tubular bags, plastic components like bottom bars, vent plugs, cell covers and rubber bushes fitted to cell covers get deformed, degraded or damaged.
Whilst it is possible to revive such batteries if they are not fully damaged, the life & performance of such batteries do get adversely affected and hence it is very important to ensure that there is no spillage of acid from fully charged batteries. Loss of electrolyte from the top of the plates in the normal course without exposing the electrodes is however different and cannot be equated to spilling.
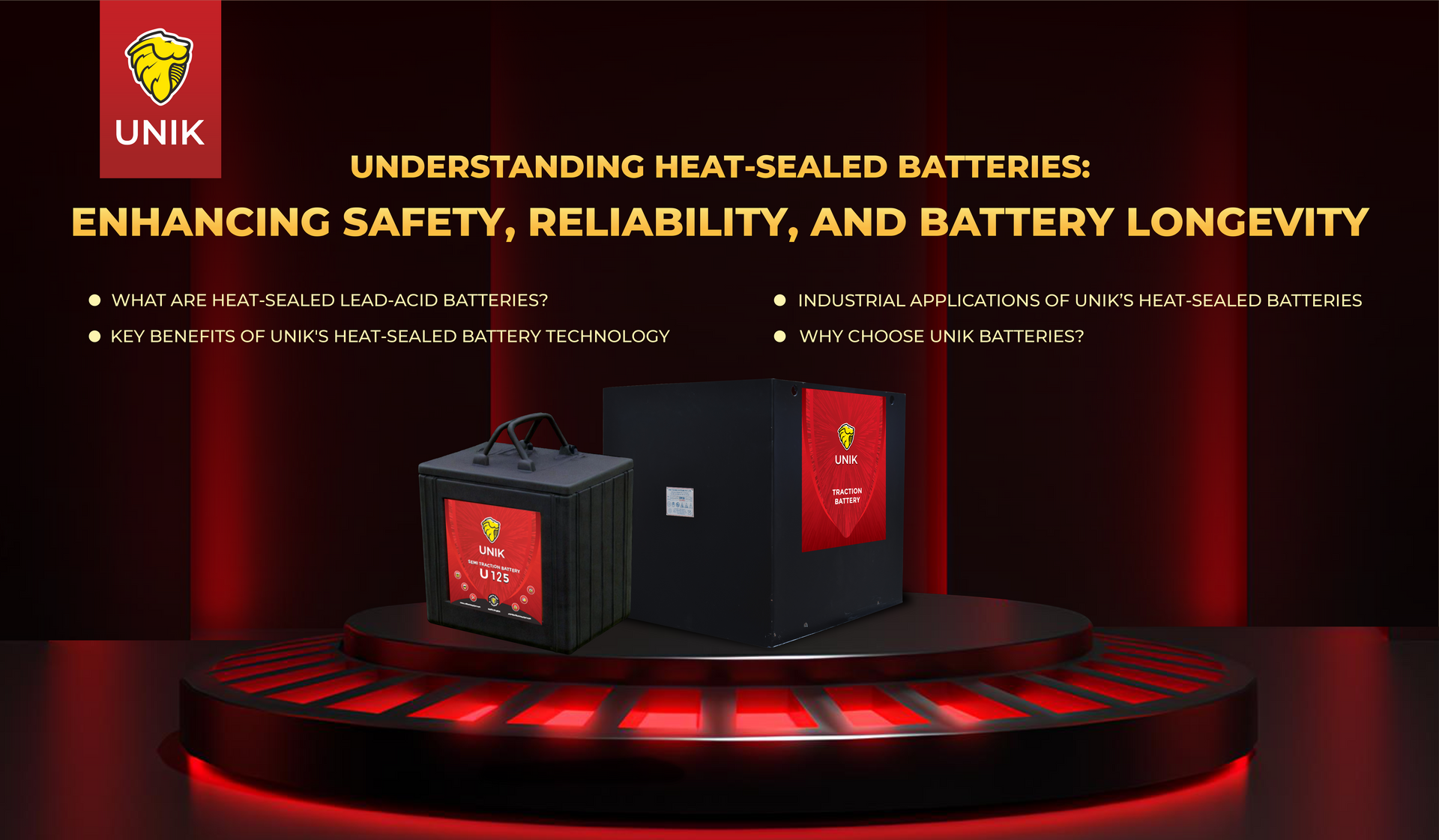
Battery safety is critical in industries relying heavily on robust, dependable power sources such as electric forklifts, golf carts, and industrial machinery. One technology significantly advancing battery safety is heat-sealed battery construction . At UNIK Batteries, we utilise advanced heat-sealing techniques to provide superior safety, reliability, and longer battery life for demanding industrial applications. What Are Heat-Sealed Lead-Acid Batteries? Heat-sealed lead-acid batteries are constructed using a specialised sealing process where battery casings are permanently bonded through heat application. Unlike traditional battery sealing methods using adhesives or mechanical seals, heat sealing creates a highly durable, airtight enclosure, ideal for demanding industrial environments. Key Benefits of UNIK's Heat-Sealed Battery Technology Electrolyte Leakage Prevention Higher resistance levels, which may impact power output. Reduced charging efficiency, resulting in longer charge times. Increased operational strain, potentially leading to faster wear and tear. Here is why winter battery maintenance is essential: Proper care reduces the risk of cell damage due to freezing temperatures. Batteries that are well-maintained offer operational efficiency. Regular maintenance extends the life of your batteries, saving on replacement costs. Taking these steps will keep your i ndustrial forklift battery in peak condition, even when temperatures plummet. Lead Acid & Lithium-ion Battery Care in Cold Weather Maintenance of Lead Acid Batteries Lead acid batteries are more sensitive to cold temperatures because their electrolyte solution can freeze, particularly when the battery is in a low-charge state. For efficient battery care in cold weather, follow these tips: Charge fully after each use as a fully charged lead-acid battery is less likely to freeze. Store batteries in a temperature-controlled environment indoors or in a heated area to protect them from the elements. Inspect the battery for cracks or leaks, as these can worsen in the cold. Lead-acid batteries need adequate water to function correctly, so check and refill water levels routinely. Clean terminals regularly to prevent corrosion and improve conductivity. Lithium-ion Battery Maintenance While lithium-ion batteries fare better than lead acid batteries in colder weather, they still require care to avoid performance drops. Follow these tips for top-notch lithium-ion battery maintenance: When starting your material handling equipment, give your battery some time to warm up just as you would allow your car battery to reach an optimum temperature before driving. Lithium-ion batteries should not be charged at sub-zero temperatures, as this can lead to permanent damage. Lithium-ion batteries are more efficient when they maintain a moderate charge level in winter between 30-80%, to reduce strain on the cells. Following these steps can help ensure that both l ead acid and lithium-ion battery maintenance routines are winter-ready. Winter can be challenging for industrial forklift batteries , but with consistent battery care in cold weather , you can protect your investment and keep your operations running smoothly. By paying attention to winter battery maintenance and adjusting your care strategies for different battery types, you can enhance battery performance and extend its life, no matter how cold it gets. Protect your operations all season long! For more tailored solutions, explore our lithium-ion battery and lead acid battery sections to find the best fit for your material handling operations. Contact us today to learn how our battery solutions can power your success.
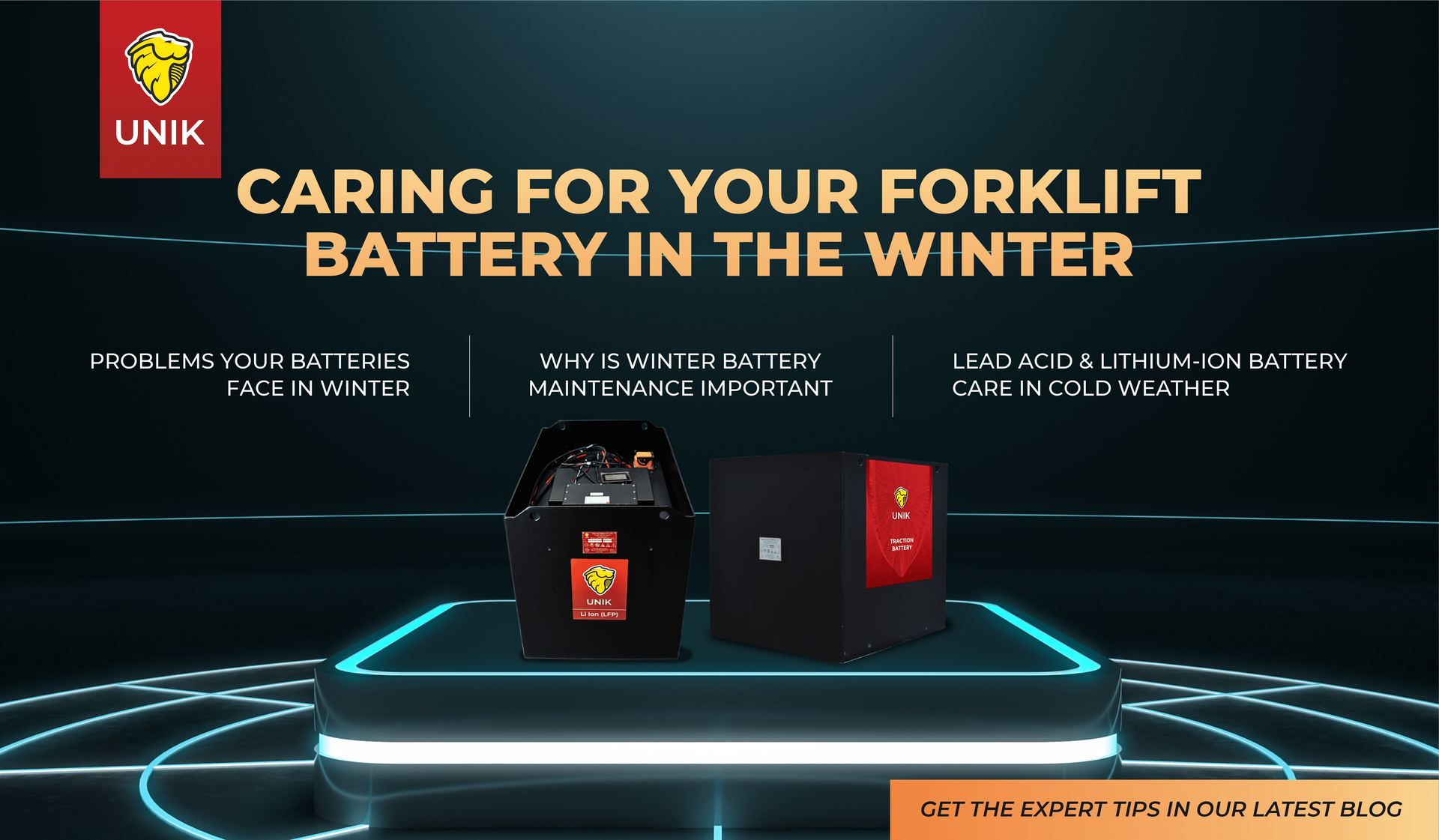
When it comes to powering industrial equipment, the choice of battery plays a crucial role in ensuring efficiency and reliability. Traction and semi-traction batteries are key players in this arena, each designed to meet specific operational needs. This blog delves into what these batteries are and their applications in industrial settings. What are Traction Batteries? Traction batteries are specialised rechargeable batteries used to power heavy-duty industrial equipment. Unlike traditional starter batteries, they are engineered to provide reliable and consistent power over extended periods, making them suitable for applications that require deep discharges and frequent recharging. These batteries are typically made up of several cells connected in series, with the most common types being lead-acid traction batteries and lithium-ion . Lead-acid traction batteries are favored for their cost-effectiveness and durability, whereas lithium-ion traction batteries are sought after for their high energy density and lower maintenance requirements. What are the Applications of Traction Batteries? Traction batteries are widely used for rigorous applications in sectors, such as golf carts, renewable energy systems, medical equipment, and power backup systems. Material handling and industrial applications benefit significantly from these batteries. Traction batteries for material handling equipment are used for powering forklifts, pallet jacks, and other material-handling equipment. The high capacity and durability of lead-acid traction batteries and lithium-ion traction batteries make them perfect for these tasks. They ensure reliable performance and longevity in demanding environments, including warehouses and factories that rely on robust power supply. What are Semi-traction Batteries? Semi-traction batteries, also known as monobloc batteries, are engineered for exceptional performance in industrial settings where consistent power is required over extended periods. These batteries are specifically designed to handle repetitive and intense cycle use. A semi-traction battery is constructed with multiple electrically connected cell compartments containing electrodes, electrolytes, terminals, and separators. These cells can be arranged in series or parallel configurations to tailor the battery's performance to specific applications. Semi-traction batteries are engineered to endure harsh conditions, including wide temperature fluctuations (-30°C to 60°C) and exposure to shocks and vibrations. What are the Applications of Semi-traction Batteries? Semi-traction batteries are versatile and provide dependable power for various applications where the energy demand is moderate and consistent, but not as intensive as in heavy industrial use. These batteries are particularly effective in settings where a reliable energy source is needed over an extended period. They may be used for less intensive off-grid solar power systems and energy storage applications. Semi-traction batteries are particularly advantageous in golf carts and industrial cleaning equipment . Golf carts benefit from the battery’s ability to endure frequent discharge cycles, vibrations, and temperature variations, providing reliable power in varied conditions. Similarly, semi-traction batteries excel in industrial cleaning equipment, such as floor scrubbers, where they provide the necessary power to operate efficiently over long periods, withstanding the rough conditions typical in industrial environments. In the world of industrial equipment, the choice between traction and semi-traction batteries can significantly impact operational efficiency and longevity. Traction batteries provide robust, reliable power for heavy-duty applications, such as material handling equipment, while semi-traction batteries offer a dependable solution for moderate energy needs, like those found in golf carts and cleaning machines. By selecting the right type of battery for each specific application, businesses can ensure uninterrupted operations, reduce downtime, and maintain consistent performance in all conditions. UNIK recognises the diverse battery needs of different industries and is here to help you find the perfect fit. Contact us today to learn how our battery solutions can power your success.
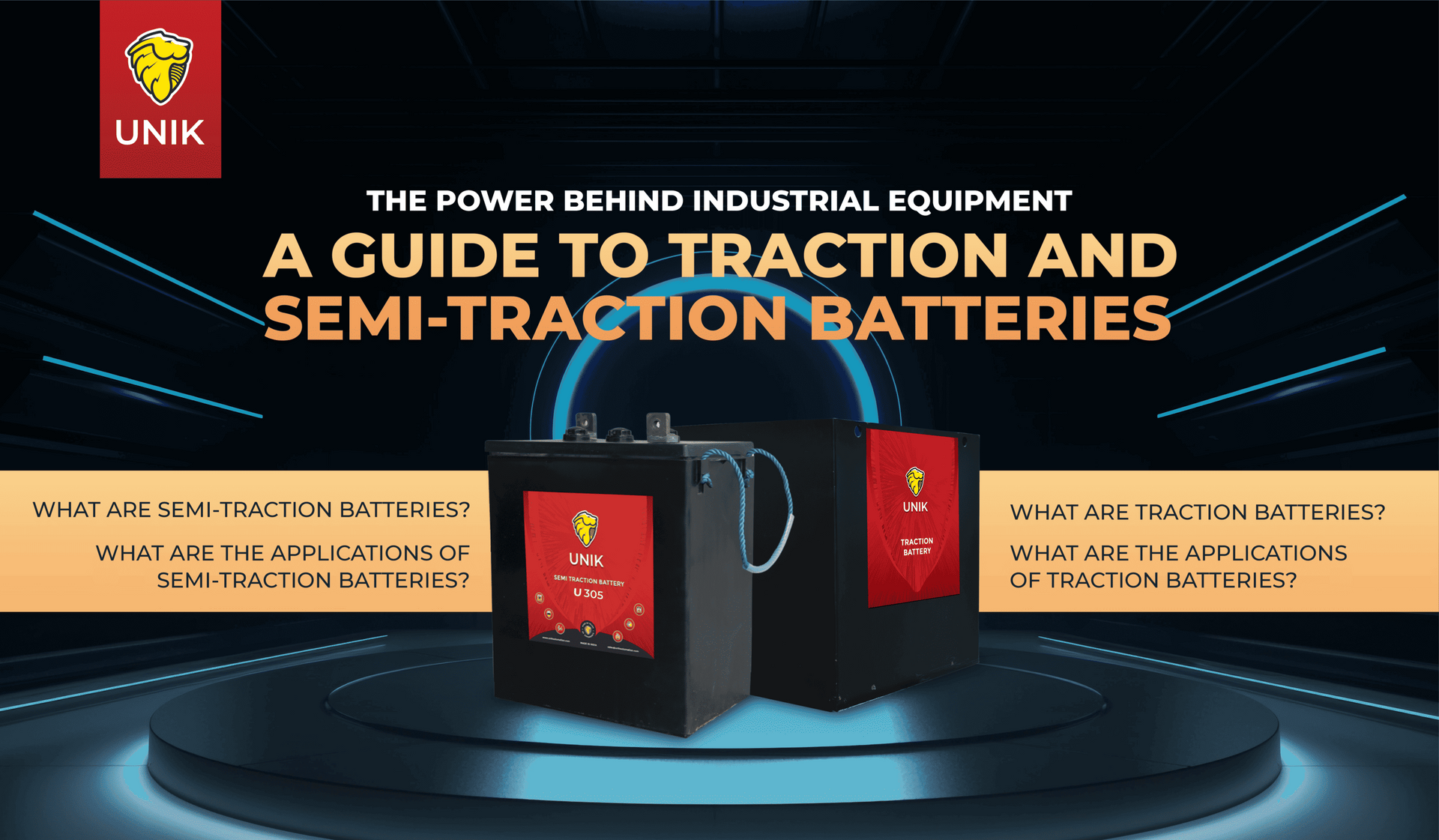
When it comes to powering industrial equipment, the choice of battery plays a crucial role in ensuring efficiency and reliability. Traction and semi-traction batteries are key players in this arena, each designed to meet specific operational needs. This blog delves into what these batteries are and their applications in industrial settings. What are Traction Batteries? Traction batteries are specialised rechargeable batteries used to power heavy-duty industrial equipment. Unlike traditional starter batteries, they are engineered to provide reliable and consistent power over extended periods, making them suitable for applications that require deep discharges and frequent recharging. These batteries are typically made up of several cells connected in series, with the most common types being lead-acid traction batteries and lithium-ion . Lead-acid traction batteries are favored for their cost-effectiveness and durability, whereas lithium-ion traction batteries are sought after for their high energy density and lower maintenance requirements. What are the Applications of Traction Batteries? Traction batteries are widely used for rigorous applications in sectors, such as golf carts, renewable energy systems, medical equipment, and power backup systems. Material handling and industrial applications benefit significantly from these batteries. Traction batteries for material handling equipment are used for powering forklifts, pallet jacks, and other material-handling equipment. The high capacity and durability of lead-acid traction batteries and lithium-ion traction batteries make them perfect for these tasks. They ensure reliable performance and longevity in demanding environments, including warehouses and factories that rely on robust power supply. What are Semi-traction Batteries? Semi-traction batteries, also known as monobloc batteries, are engineered for exceptional performance in industrial settings where consistent power is required over extended periods. These batteries are specifically designed to handle repetitive and intense cycle use. A semi-traction battery is constructed with multiple electrically connected cell compartments containing electrodes, electrolytes, terminals, and separators. These cells can be arranged in series or parallel configurations to tailor the battery's performance to specific applications. Semi-traction batteries are engineered to endure harsh conditions, including wide temperature fluctuations (-30°C to 60°C) and exposure to shocks and vibrations. What are the Applications of Semi-traction Batteries? Semi-traction batteries are versatile and provide dependable power for various applications where the energy demand is moderate and consistent, but not as intensive as in heavy industrial use. These batteries are particularly effective in settings where a reliable energy source is needed over an extended period. They may be used for less intensive off-grid solar power systems and energy storage applications. Semi-traction batteries are particularly advantageous in golf carts and industrial cleaning equipment . Golf carts benefit from the battery’s ability to endure frequent discharge cycles, vibrations, and temperature variations, providing reliable power in varied conditions. Similarly, semi-traction batteries excel in industrial cleaning equipment, such as floor scrubbers, where they provide the necessary power to operate efficiently over long periods, withstanding the rough conditions typical in industrial environments. In the world of industrial equipment, the choice between traction and semi-traction batteries can significantly impact operational efficiency and longevity. Traction batteries provide robust, reliable power for heavy-duty applications, such as material handling equipment, while semi-traction batteries offer a dependable solution for moderate energy needs, like those found in golf carts and cleaning machines. By selecting the right type of battery for each specific application, businesses can ensure uninterrupted operations, reduce downtime, and maintain consistent performance in all conditions. UNIK recognises the diverse battery needs of different industries and is here to help you find the perfect fit. Contact us today to learn how our battery solutions can power your success.