Dry Batteries Versus Wet Batteries: Which One is Best for Your UPS System
Why is Choosing the Right UPS System Batteries Important?
During power outages and blackouts, Uninterrupted Power Supply (UPS) backups are crucial in operational efficiency and energy self-reliance. In India especially, one witnesses seasons of frequent power fluctuations, particularly in the monsoon and summer months, making UPS systems an inseparable part of modern industries.
The choice of a correct battery is the most essential component of a UPS, which warrants making an informed decision while choosing UPS system batteries.
Factors such as maintenance, lifespan, power outputs, and depth of discharge, among others, play a significant role in determining the ideal battery life for your UPS system.
Lead acid batteries or wet batteries are predominantly used as UPS system batteries. However, Absorbed Glass Mats (AGM) or dry batteries are becoming increasingly popular along with lithium-ion batteries.
This blog compares the two batteries to help make an informed decision for various UPS system applications.
The Composition of Wet Batteries Versus Dry Batteries
A wet battery or a lead acid battery comprises of lead plates suspended in a tank of diluted sulphuric acid.
However, an Absorbed Glass Mat (AGM) or dry battery contains a glass mat separator that wicks the electrolyte between the lead plates. This material's structure allows the absorptive glass mat to absorb the electrolytes and retain them in a "dry" or suspended state instead of being in a free-flowing liquid form.
What are the Maintenance Procedures and Advantages of Wet Batteries?
While lead acid batteries are considered cost-effective and tried and tested UPS system batteries, they also require maintenance procedures, especially in larger UPS systems.
Considering the nature of the liquid sulphuric acid in these batteries, thorough preventive maintenance is required every quarter.
Ventilation and the position of these batteries are of utmost importance for operator safety. The electrochemical processes that occur within the battery to generate a current produce a gaseous material by-product. These gases must be expelled efficiently through the battery's vents to maintain an optimum internal temperature within the cell. Therefore, the foremost steps in battery maintenance is as follows:
- Free the battery of all dust and debris, particularly around the air vents.
- Lead acid batteries stored for future use must be kept in a cool environment upright to avoid any acid leakage.
- The battery should be checked for any leaks that can compromise the safety of the UPS system.
Once these preliminary steps are complete, the cables can be tightened and cleaned.
The most significant maintenance procedure typical to wet batteries is topping up of the electrolyte solution. This solution comprises of sulphuric acid diluted with demineralized water. The ratio of the two liquids in the solution must be calculated and filled to precision as per the manufacturer's guidelines.
Despite being bulky and requiring maintenance, these batteries offer many benefits, including higher power outputs, resistance to overcharging, and deeper discharge.
What are the Maintenance Procedures and Advantages of Dry Batteries?
Dry batteries require less maintenance and are more versatile as they can be operated in mobile operations. Their lifespan can be extended with simple practices like cleaning and good ventilation, as they are more prone to overheating due to a starved electrolyte construction.
Store these batteries away from windows or direct heat sources to maintain optimum temperature in the cell.
While these batteries are more expensive and need to be discarded once they stop supplying current, they also have numerous benefits that can be applied to specific requirements.
Dry cells produce energy more efficiently. Although expensive, the less rigorous maintenance saves time and operational efficiency. Moreover, these batteries offer higher operator safety and are less likely to result in accidents.
In conclusion, deciding between wet (lead acid) and dry (AGM) batteries for UPS power supply hinges on key considerations. Though bulky and demanding rigorous maintenance, wet batteries offer higher power outputs and resilience to overcharging. Conversely, dry batteries require less upkeep, cater to mobile operations, and boast efficient energy production. The choice should align with specific application needs, balancing maintenance preferences, operational efficiency, and safety considerations for reliable industrial UPS performance amid power fluctuations and outages.
At UNIK, we specialise in manufacturing a vast range of high performing dry charged batteries and wet batteries that cater to an array of industrial applications and standards.
Contact our team of experts to find the right battery for your industrial needs.
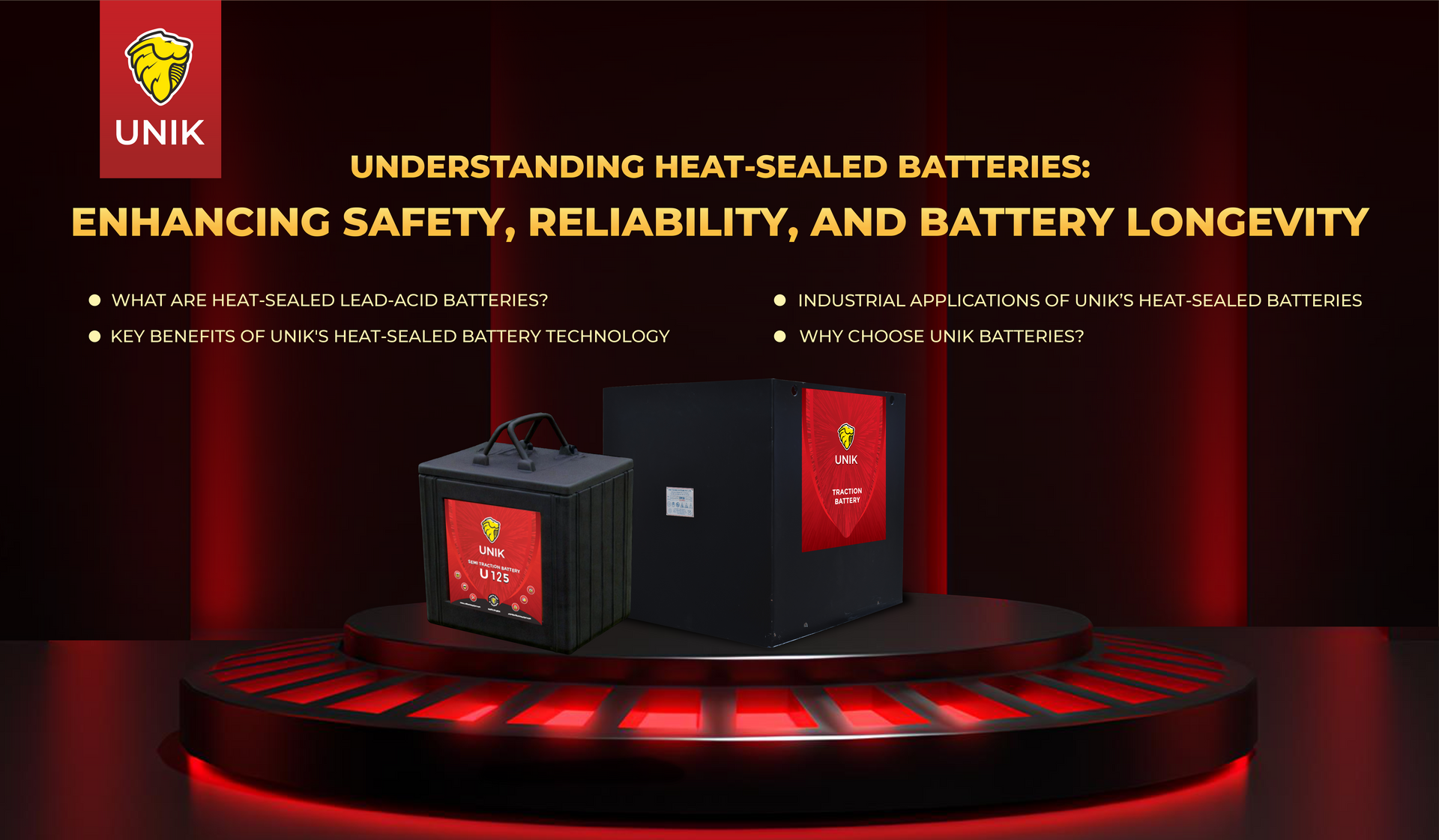
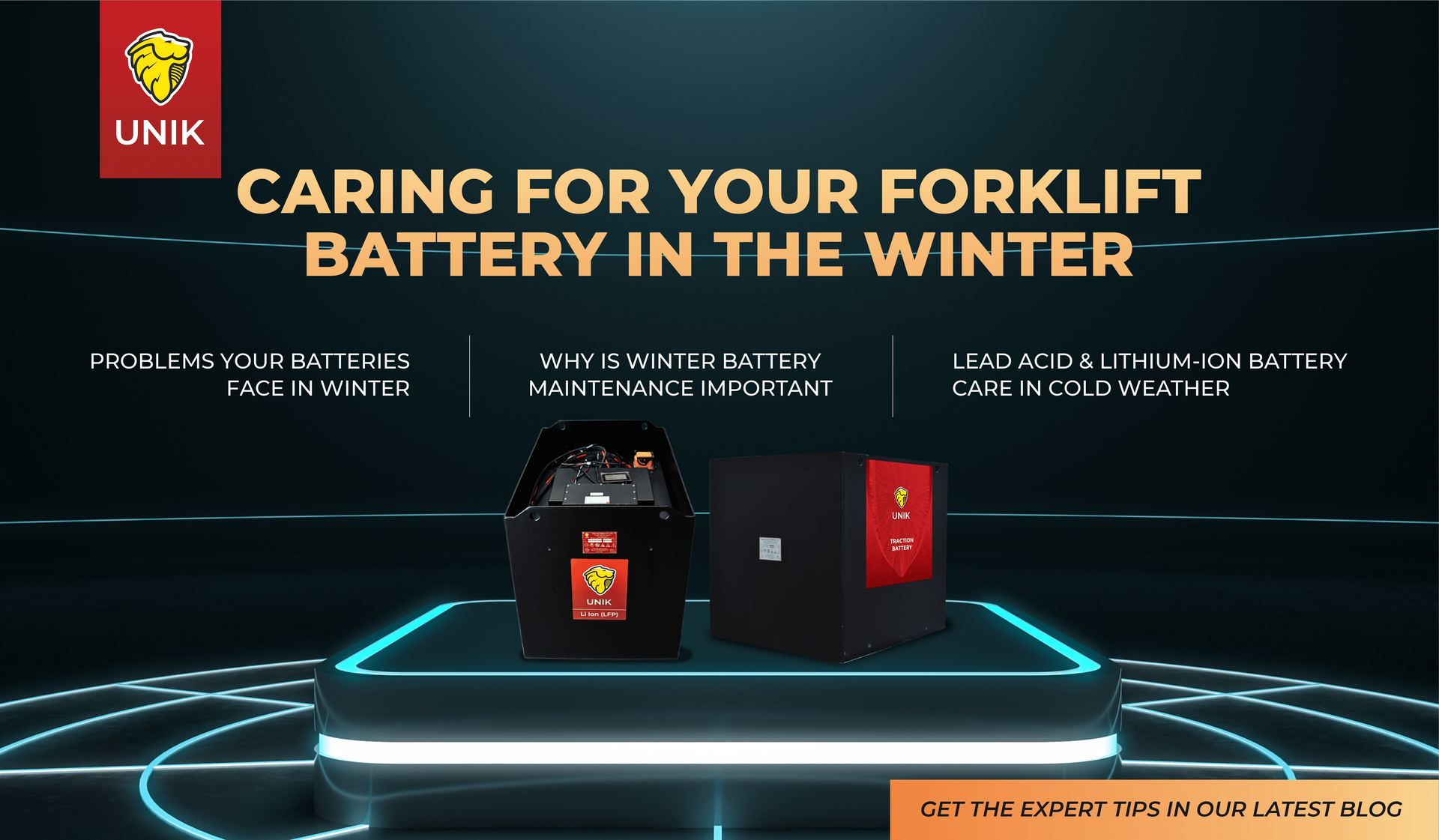
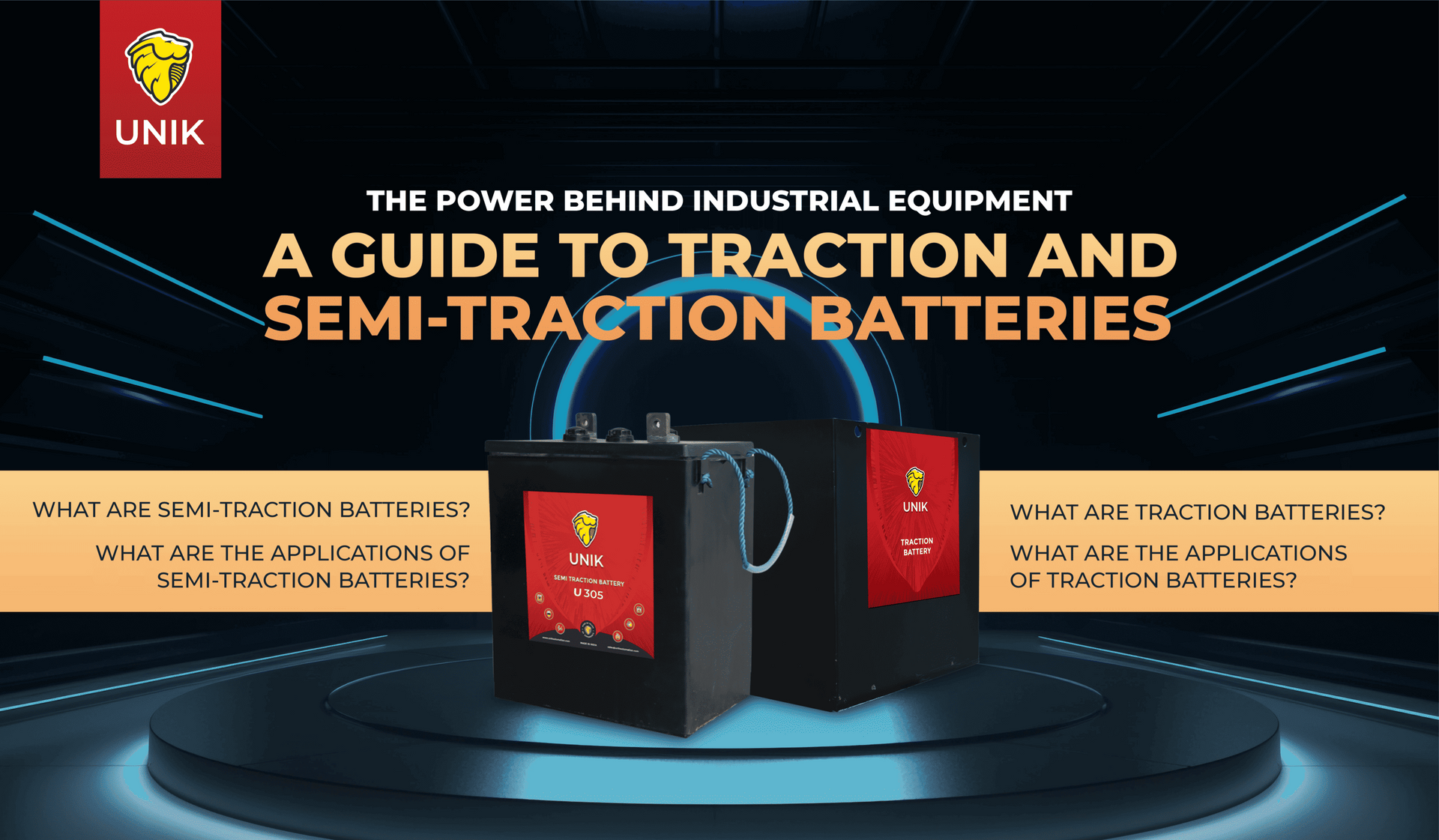